The U.S. Centers for Disease Control and Prevention (CDC) estimates that 48 million cases of foodborne illness results in 128,000 hospitalizations and 3,000 deaths on an annual basis, and 70 percent of investigations are unresolved at the state level.
The root cause of such illness ranges from accidental contamination (such as failure to maintain appropriate hygienic procedures of individuals, allergen management, equipment that are in contact with food, etc.) to economic adulteration and even deliberate contamination (such as terrorism related), in this post 9/11 era (Figure 1).
Businesses should review their current recall execution capability and use the passage of the Food Safety Modernization Act (FSMA) as an opportunity to evaluate and improve upon current recall management practices, as well as be ready to comply with Section 103 of the Act “Hazard analysis and risk-based preventive controls,” which requires registered facilities to perform a hazard analysis and implement a preventive controls plan which contains, among other controls, a recall plan.
Facts:
• Average recall costs are $10M (excluding brand damage and lost sales)
• 48 percent of companies surveyed can execute a recall in hours, 52% can execute recall in days/weeks
• The cost of food poisoning in this country comes to $14 billion a year, according to a July 2012 study published in the Journal of Food Protection
• Government regulators are increasingly concerned about the time taken to respond to food-related emergencies, as consumer trust in food becomes more fragile as evidenced by the 2011 FSMA post 9-11
• The U.S. population is becoming more susceptible to foodborne illness—20 percent to 25 percent of the population is comprised of the elderly, children and pregnant women—the highest risk demographics
Impact to companies could vary depend on type of recall (Table 1). To evaluate their current recall processes companies should perform the following:
• Simulate a product recall exercise to assess where gaps may exist that can inhibit or prolong product recalls
• Evaluate current food defense programs for adequacy compared with government agency guidance (vulnerability assessment tools are available on FDA.gov)
• Enable lot level tracking in their warehouse management systems to trace lot level allocation to specific orders/customers/channels to create a targeted approach to product recalls, instead of a broad stroke approach
• Leverage systems and processes that trace products, ingredients, raw materials, manufacturing and labor assets through-out the supply chain—from procurement through delivery
• Maintain accurate customer and contact list to ensure recalls can be initiated quickly without latency
• Leverage direct to customer engagement mechanisms, such as social media, customer loyalty card information, etc., to ensure tighter/faster recall times
• Update food safety and food defense plans including hazard analysis, preventative controls, verification and testing
• Review records maintenance and access procedures—a critical element for traceability
• Know your suppliers and their suppliers (not just your distributors and customers)
• Enable collaboration across trading partners on a common platform
Companies need a traceability solution that is based on the three tenets of IT-enabled information transformation that are key to administer a robust food safety regime:
• Information Capture
• Information Storage and Processing
• Information Sharing
Information Capture
Gathering transaction data from multiple supply chain touch points (varying from manufacturing plant systems to quality control data from external auditors) is the first step towards ensuring food safety compliance. Solution components include:
• Data collection process standardization
• Automated data feeds from manufacturing plants
• Helpdesk-enabled data collection and digitization
• Remote data capture (field apps, field device Integration)
Information Storage and Processing
The data acquired across the supply chain are in a raw format and needs to be transformed into insightful information in order to derive business decisions. Enterprise integration helps build capacity and proper storage of this data by linking them to the appropriate business functions (e.g., material safety data sheet )getting attached with every sales order generated from an enterprise system).
Information Collaboration
The most vital part of the food safety and traceability capability is the ability of all partners in the supply chain to predict and pre-empt food contamination in order to minimize the time to recall. Wipro solution prescribes an IT-enabled platform for all supply chain stakeholders. Platform capabilities include:
• Threshold based alerts
• Supplier performance dashboards
• Product batch traceability
• Social media analytics
• Incident management desk (food recall management)
Through technology enabled solutions, a wide range of food safety requirements such as production quality inspection, supplier quality management, calibration management, document retention management, audit management and integration with lab information management systems can enable traceability, visibility and supply chain security to enable real-time monitoring of the entire value chain. Additionally, a solution with predictive analytics can allow tighter controls to ensure supply chain security and integrity.
Bob Patel is principal and practice head, consumer goods, and Umesh Tejwani is head, business solutions, consumer goods, of Wipro Technologies. Sriniwas Acharya is a principal consultant, agribusiness practice, RCTG, Wipro.
Product Recall and Traceability
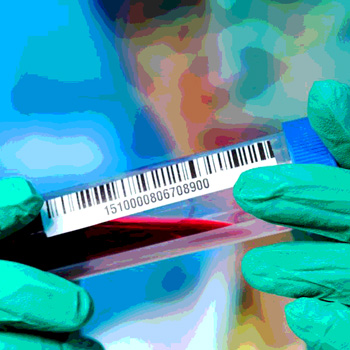