The Product Traceability Initiative (PTI) was created by the Produce Marketing Association, Canadian Produce Marketing Association and the United Fresh Produce Association, in conjunction with the produce industry (suppliers, retailers, wholesalers, foodservice). The initiative envisions supply chain-wide adoption of electronic traceability for every case of fresh produce shipped for consumers.
Standard identification allows members of the produce supply chain to easily scan, obtain and register the data encoded in the bar code. In case of a recall, the source and span of affected produce can be quickly identified to reduce human risk. Products unaffected by recalls can be easily separated toreduce business risk.
Barcode print quality is fundamental to accurate identification. If a barcode doesn’t scan, packagers and retail customers must manually type in the human readable numbers. This process is time-consuming and prone to input errors. Retailers may reject cases that do not have clear bar codes and some may reject full pallets, leading to costly rework and possibly lost merchandise.
To succeed in implementing the PTI, it is important for producers and packagers to choose the rightprinting solution for case identification. Common agreement on the printing technology and bar code readability with all business partners is recommended so that expectations are aligned and met.
What Is the Produce Traceability Initiative (PTI)?
The retail and foodservice markets receive fresh produce cases from many suppliers. These cases typically contain different types of information and formatting. Some contain only the product’s name, some include date and lot number, and others include a bar code. Currently most—but not all—produce can be tracked from company to company according to the “one step forward and one step back” requirements of U.S. Bioterrorism Act of 2002 (internal traceability). There were no standards for case identification and, as a result, recalls were slow and often left store shelves bare of product.
By having product data and the lot/batch represented by a bar code on the side of each fresh produce case, and having this data registered up the supply chain, those in the industry can now trace the produce back to its origin faster and more efficiently. The result is higher consumer confidence in the produce supply chain.
The basic standard case identification recommended to the industry is composed of a GS1-128 bar code containing a GTIN-14, which contains the GS1 Company prefix and the item reference number. Additionally, it should include a lot/batch number and a voice-pick code, which is a four-digit number, calculated using the GTIN, lot code and optional date.
GS1 is an international not-for-profit association dedicated to the design and implementation of global standards and solutions to improve the efficiency and visibility of supply and demand chains globally and across sectors.
PTI-Compliant Case Printing Methods
To comply with PTI standards, printing technology options includehigh resolution large character direct case coding printers and thermal transfer label printers. These two technologies differ in their printing methodology, benefits and limitations.
Direct Case Coding Printers. Large character ink-jet printers code directly onto the side of corrugated cases and allow on-line printing according to the produce being packed. Some are capable ofprinting high resolution text, bar codes and logos, resulting in a pre-printed look.
Benefits include a small equipment footprint and easy integration into a production line. Ink can be replaced without stopping the production line. And, these printers offer a lower cost per print when compared with thermal transfer printers’ labels and ribbons. However, they will are designed to print on porous substrates including corrugated cases and paper surfaces.
Thermal Transfer Label Printers. This printing method is based on a thermal printhead and thermal transfer ribbon. The print information is prepared in the thermal printhead and individual printing dots are heated as required. The colored pigment in the ribbon is then transferred onto the label.
Case identification thermal transfer printers can be installed in a tabletop format where the label is printed and hand-applied to the case. The system can also be built to serve as an automatic label printer and applicator, allowing automatic on-line printing.
Benefits include good print contrast and readability independent of the substrate color or porosity. Printing is done separately from case movement on the production line. However, the overall cost of ownership is higher than direct case coding and there’s also potential for labels to be misapplied or dropped off the case as it moves through the supply chain. And replacement and changeover of labels and ribbons require more downtime.
Factors to Consider in Choosing a Print Method
The PTI calls for every case?corrugated, returnable plastic containers, bags and bins?containing fresh produce for sale to consumers and foodservice to have standardized product identification. In selecting the most appropriate print technology, the following factors should be considered:
Cost of ownership. With direct case printing, a constant supply of ink is needed whilethermal transfer label printers requiresupplies of labels and ribbons. A simple calculation can be done comparing costs for consumables, leading to the conclusion that in general, the cost per print using ink is less than the cost per print to print a label.
For example, let’s assume 1,200,000 cases per year are produced. Label cost is $0.02 each, ribbon cost is $0.01 per label and cost of ink for direct coding is $0.007 per message. The table below offers acost comparison between thermal transfer and direct ink-jet technologies.
Based on the assumptions given, the cost of consumables with direct ink-jet technology is approximately one-fifth of the cost of consumables when printing with thermal transfer technology.
Case substrate porosity. For corrugated cases and trays, if the substrate is porous, direct ink-jet printing is a good option due to its low cost of ownership. If the substrate is non-porous?a varnished case, for example?a thermal transfer printed label is recommended. In addition, labels are the best solution for returnable plastic containers, bags and bins.
Case packing environment. The environment in which the produce is being packed is also a deciding factor. Is it packed in the field, in a shed? What are the temperature conditions? Are lines washed down regularly? Different bar code printers are suited for different packaging environments. Most importantly, the printers need to be robust and efficient enough to print in the required environment and meet the desired bar code quality.
Production line configuration. Case identification is usually the last process in a production line, so relevant questions include: Is space a limitation in the line? Is there a conveyor? A case sealer? Depending on available space and how cases are handled at the end of the production line, a direct ink-jet printer or thermal transfer label printer can be used. While direct ink-jet printers can be integrated more easily into the production line, good bar code quality requires that a belt conveyor be used and that the cases are correctly oriented and guided.
Check Bar Code Readability
One of the best ways to ensure that cases containing readable bar codes reach the market is the addition of a bar code check stage after the case has been printed. This does not have to be complex?a simple bar code scanner correctly specified for theproduction line, together with a reject system, will accomplish the task. Every case should be read to confirm readability.
For advanced control, the bar code scanner can be set up with the printer to confirm that the bar code printed is the one requested. Bar code scanners can also be linked to network management software so that the printed data is logged and used for data control and case recall, a critical component of any PTI project.
The produce industry and consumers alike will benefit from compliance with the PTI standard label. Printer specialists can help to determine and select the best printing technology to print bar codes and messages that are suitable for produce traceability.
David Freed is regional product manager, Videojet. To learn more about coding techniques and printing methodologies for meeting PTI standards, visit: www.videojet.com/pti.
Compliance with the Produce Traceability Initiative
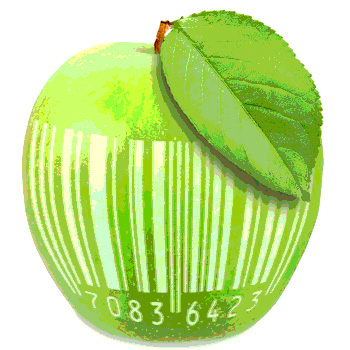